Maintenance service
The services for equipment support have national coverage, we reach wherever your machinery is operating. Likewise, we make sure to provide you with all the necessary recommendations for the correct operation of the equipment, to maximize its useful life, ensuring the profitability of your investment.
Receive the support you deserve, contact our customer service and schedule your maintenance. For more information on click here
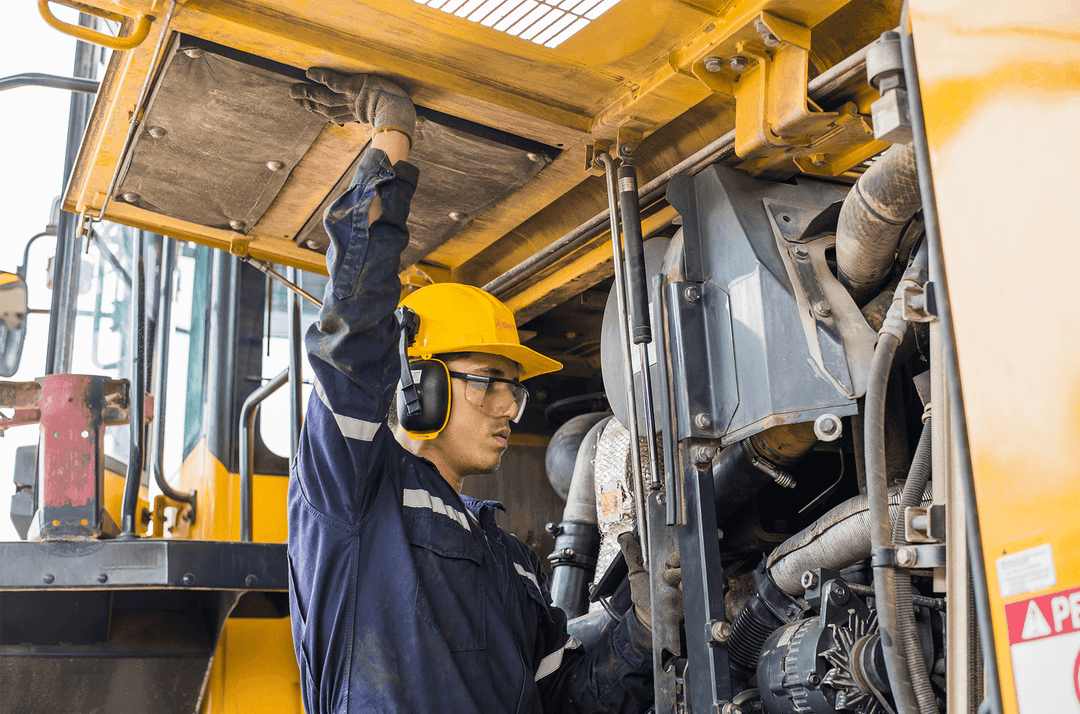